In an increasingly interconnected world, supply chains face more challenges than ever. Disruptions from global pandemics, natural disasters, or trade wars highlight the need for businesses to shift from reactive, problem-solving modes to proactive, anticipatory strategies. The transformation from reactive to proactive supply chain operations is not just a competitive advantage—it’s becoming a necessity for businesses aiming for resilience, agility, and long-term success.
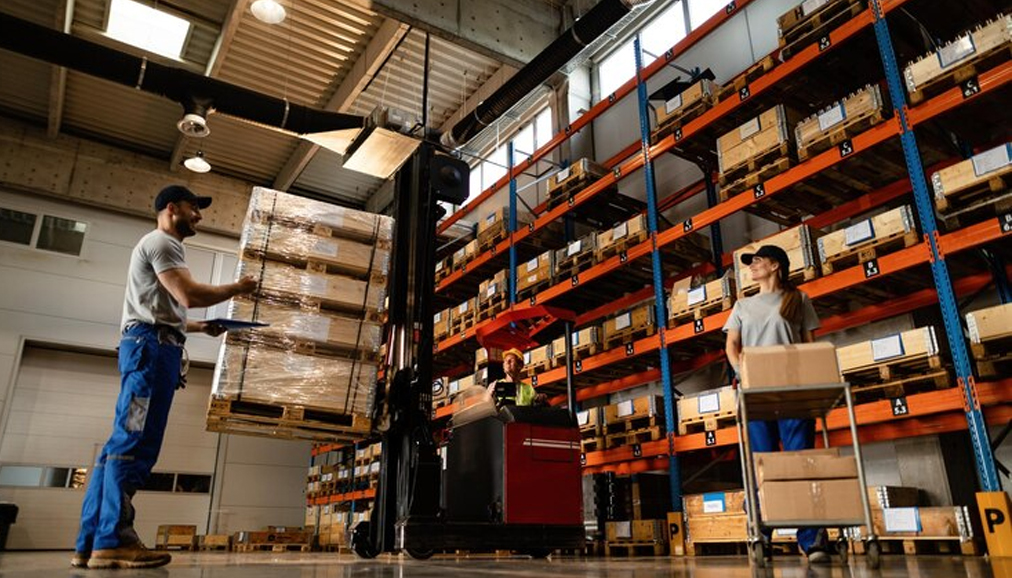
The Reactive Supply Chain: Challenges and Limitations
The Reactive Supply Chain: Challenges and Limitations
Reactive supply chains are characterized by their "firefighting" approach—where businesses only respond to disruptions after they occur. This method has significant limitations:
- Lack of Visibility: Reactive operations often suffer from poor visibility into the supply chain, meaning issues like delayed shipments or inventory shortages are only noticed when it’s too late.
- Inconsistent Demand Fulfillment: Inability to predict fluctuations in demand often leads to overstocking or stockouts, affecting profitability and customer satisfaction.
- Increased Operational Costs: Emergency responses to disruptions can include expedited shipping, costly stock replenishment, or penalties for late deliveries.
- Strained Supplier Relationships: Reacting late to disruptions can cause tension with suppliers who may struggle to meet last-minute demands or resolve quality issues on short notice.
- Inflexibility: A reactive supply chain is often unable to adapt quickly to changes in the market or external environment, resulting in missed opportunities and potential revenue loss.
The Case for a Proactive Supply Chain
A proactive supply chain model aims to preemptively address potential issues before they disrupt operations. The benefits of this approach include:
- End-to-End Visibility : Proactive supply chains leverage advanced technologies like IoT, RFID, and cloud platforms to provide real-time data on inventory, production status, and transportation logistics.
- Demand Predictability: Predictive analytics enable businesses to anticipate market demand fluctuations, thus ensuring optimal stock levels and improving order fulfillment.
- Agility and Flexibility: A proactive supply chain is equipped to pivot quickly in response to market changes, regulatory shifts, or supplier issues. This allows companies to seize new opportunities or mitigate risks without significant disruptions.
- Cost Efficiency: Proactively identifying inefficiencies (like bottlenecks or delays) leads to smoother operations and reduced costs. Companies can move from reactive rush orders and expensive contingencies to streamlined, cost-effective practices.
- Customer-Centric Operations: Meeting or exceeding customer expectations becomes easier when a business anticipates their needs. Proactive operations mean fewer delays, higher product availability, and better service delivery.
Key Components of a Proactive Supply Chain
Technology-Driven Transformation Proactive supply chains rely heavily on digital transformation to improve visibility, efficiency, and decision-making capabilities. Key technologies include:
- 1. Predictive Analytics: These tools analyze historical data to forecast future demand, predict potential disruptions, and suggest optimal actions. For instance, algorithms can predict weather patterns or supplier delays, allowing businesses to adjust their logistics accordingly.
- Artificial Intelligence (AI) and Machine Learning (ML): AI can optimize everything from demand planning to route optimization, while ML continuously improves these processes by learning from new data.
- Internet of Things (IoT): IoT sensors provide real-time updates on the location and condition of goods, helping to monitor and adjust supply chain activities instantly.
- Digital Twins: A digital twin of the supply chain creates a virtual model that allows businesses to simulate various scenarios, helping identify vulnerabilities and test solutions before real-life disruptions occur.
2. Demand Forecasting and Inventory Optimization Proactive supply chains invest in advanced demand forecasting systems, which use a combination of historical sales data, market trends, and external factors (such as economic indicators or geopolitical events). This enables businesses to anticipate customer demand and adjust their production and inventory levels accordingly. By accurately forecasting, companies can:
- Reduce the risk of overstocking or understocking.
- Improve supplier lead times.
- Optimize inventory management, reducing carrying costs and wastage.
3. Collaborative Supply Chain Networks A proactive supply chain requires strong collaboration across the entire network—from suppliers to manufacturers, distributors, and customers. Implementing collaborative tools like Vendor Managed Inventory (VMI) systems and cloud-based platforms can help synchronize supply chain partners, enabling better communication and coordination.
- Real-Time Data Sharing: Sharing real-time data with suppliers helps in anticipating stock shortages and allows businesses to adjust production plans, preventing bottlenecks.
- Strategic Supplier Partnerships: By creating long-term partnerships, businesses can develop more resilient supply chains. Suppliers that are integrated into a proactive model can adjust their own operations to align with the business’s needs.
4. Risk Management and Contingency Planning Proactive supply chains emphasize risk identification and mitigation. To stay ahead of disruptions, companies need a structured risk management framework that includes:
- Risk Assessment: Mapping out potential risks such as geopolitical instability, cyber threats, or transportation disruptions. Companies can use risk monitoring tools to stay alert to emerging threats.
- Scenario Planning: Running simulations (via digital twins or other tools) to predict how certain risks would impact the supply chain and developing contingency plans.
- Diversified Sourcing:A proactive strategy includes diversifying suppliers and transportation modes to avoid over-reliance on a single source. This reduces the impact of potential bottlenecks and disruptions in one region.
5. Agile Supply Chain Models Proactive supply chains often overlap with agile supply chain principles. By focusing on agility, businesses are better prepared to react quickly to unforeseen circumstances. Characteristics of an agile supply chain include:
- Flexibility in Manufacturing and Logistics: The ability to shift production between plants or adjust transportation routes to avoid delays.
- Shorter Lead Times: Reducing the time it takes to produce and deliver goods allows for more reactive capacity while remaining proactive in planning.
- Dynamic Resource Allocation:Proactively monitoring resources like staff, production capacity, and logistics ensures rapid adjustments when demand fluctuates.
Case Study: How a Proactive Supply Chain Transformed a Business
Take the case of a global electronics manufacturer that traditionally operated on a reactive model, leading to delayed product launches and missed market opportunities. By transitioning to a proactive supply chain, they implemented AI-driven demand forecasting, integrated IoT devices across their warehouse and transportation fleet, and established closer partnerships with key suppliers.
The results were significant:
- Reduced stockouts by 20% as predictive analytics anticipated inventory needs.
- Cut emergency shipping costs by 30% by optimizing delivery routes and planning for potential disruptions like port strikes or weather-related delays.
- Increased customer satisfactiondue to faster and more reliable order fulfillment.
Conclusion: Building the Supply Chain of the Future
The transformation from a reactive to proactive supply chain is not a one-time project but a continuous journey. Businesses need to embrace digital tools, foster collaboration, and develop a risk-resilient culture to stay ahead of future disruptions. In doing so, they will not only enhance operational efficiency but also deliver superior customer experiences and strengthen their competitive edge.
By anticipating problems before they arise and leveraging the power of advanced technology, businesses can transform their supply chains into proactive, adaptive systems that thrive in an unpredictable world.